The knitty gritty of knitwear.
Interview & more with Sue Benfield, Knitwear Design & Production Consultant
Above from left: Sue’s knitting studio in upstate, NY; the Rachel Antonoff Sosia cardigan; one of many we worked on together there; Sosia technical sketch; & Sue & (one of) her cats, Murray.
It isn’t every day you get to learn the ins and outs of knitwear from a professional. I’ve been lucky enough to experience this privilege by having Sue Benfield as a friend and colleague for seven years. This week, we chatted about her 40 years of experience in the field of knitwear and advice on the subject of what makes a good sweater. Sue is a Knitwear Design & Production Consultant, knitting connoisseur, and general creative tinkerer. Although a Brit, Sue lives in upstate New York with her former-rockstar, current architectural-contractor husband and they are owners to not one, but, eight cats. Sue developed and hand-knit my design for my wedding day sweater (see below for fun in progress and finished product photos); and did the same for our beautiful deadstock merino Joan Hoods for Villeine. Read my interview with Sue below, with a focus on cotton knitwear since it’s summer, after all. Technical note for the reader: overlock/merrow is a machine edge finish and in the case of knitwear, indicates a cut-and-sew process was used, instead of the ENTIRE garment being completely knitted together.
Tell me a bit about your experience with knitting and what got you started in the world of knitting.
I’m like a lot English people of my generation; everybody used to knit. So you just kind of grow up with the skill…and whichever direction your life takes you, you’ve always got this really well-honed ability to do a lot of things with a couple of knitting needles. I did an academic degree but used to knit constantly. Then I discovered knitting machines and a friend at the same time happened to have a big win on the horses…so it was very kind of, like, fate. And he bought me a knitting machine. And I just thought: “oh my God, this is incredible!” So that’s how I got into hand-frame knitting.
Soon after that, Covent Garden craft market opened in central London. At first, it was full of very serious craftspeople from the big art colleges in London. There were quite a few knitters; so I was there for a few years selling sweaters. I had a little studio…I was reminded recently of Thatcher’s Enterprise Allowance Scheme which gave people a wage to keep them off the dole; it was like a guaranteed income if you started a business. Central London at that time was so full of people with small businesses, basically getting paid by the government to pursue their creative interests! A lot of successful fashion people came out of that era. It was a creative time in London…I had a great studio in Old Street…Later on I came to New York in 1989 for a vacation, got offered a job and met the guy I married. Suddenly I was living in New York and working in the industry.
*Murray the cat enters*
What are you working on right now with knitting?
I have a small group of favorite clients, such as Rachel Antonoff, 4 Objects and of course Villeine who are keeping me busy with new projects. Besides knitting, there’s currently a lot of netting and knotting going on.
I keep my archive and machinery in the Makers of Manners workshop above Chris Gordon’s Mattice Boutique in Oak Hill NY. I just completed the knitwear portion of his Fall/Winter women’s collection which will be manufactured on site and have a “made upstairs” label.
For my own research I’m developing some unlined tailored garments which consist of multiple engineered knit components, stitched together rather than looped. Meanwhile I’m waiting for the bulrushes in my pond to wither so I can have a go at some Japanese Zori-style straw sandal weaving. Legs and feet-centric textiles seem to be trending, don’t they?
We’ve worked together at Rachel Antonoff and did some development in Peru. Why is Peru a great country for knitting and sourcing cotton yarns?
One of the main reasons people go there is because the yarn is so great. Also, the textiles industry in Peru has been very altruistic and managed to pull a lot of people out of bad financial and social situations. It’s actually very difficult to find a knitting company there that isn’t very progressive about hiring women, or being women-owned–it’s very philanthropic. And also they’re very good knitters. They’ve got a very good cultural/trade office in the city with a great program which often pays for people to go to Peru, go to the big Trade Show there every year. You can get a lot of handwork done which isn’t as easy as it used to be in some other countries now. There seems to be a lot of training offered to people There is a really nice variety of high quality yarns, and you can also produce very small quantities [of sweater units]. And the people are incredibly welcoming, friendly and efficient. And the food is incredible! Lima is just like the best place with the best drinks–it’s just great!
If someone is looking for a high quality cotton sweater, what does a term like “Pima” cotton really mean?
In Peru, they use Pima cotton which is of a really high quality with very long fibers. It absorbs color nicely, washes well and has a very soft hand feel. They also know how to spin and knit with it there. Cotton is such a static fiber, it has to be knitted by people who have experience getting the tension right, that kind of thing…[Static fiber meaning: cotton fiber doesn’t have any natural recovery; it stays put].
What is a good way to care for / launder a cotton sweater long term?
Years ago I would have said “never put it in a washing machine”, but of course washing machines are so much more efficient nowadays. I put practically everything in the washing machine now. You’ve always got a decent, gentle cycle. Lay flat to dry–never hang a sweater! A lot of the time when I’m actually knitting, I’m knitting prototypes so I knit hardly anything that I don’t wash. Just make sure you’ve got some designated towels because the rolling in the towel thing is like magic (unless you’ve got a spin dryer) but even then, I prefer to roll sweaters in a towel and stand on it to get the excess moisture out. You can also get those netted drying stands for laying damp garments over.
So few people know what “fully-fashioned” knitwear means; can you describe in layman’s terms?
Fully-fashioned knitwear came first [versus cut-and-sew]. Basically you’re shaping the component part as you knit by either increasing or decreasing the edge; so you determine the curve of the armhole, neckline, etc as you go. When you cast off the last stitch, you’ve got a perfectly shaped sleeve or front or back, as opposed to knitting pieces of fabric to cut shapes out of.
I’ve had nothing against cut-and-sewn knitwear in the past, but now of course it’s hard to stomach the waste involved. [As a knitter], you can get very blinkered about traditional methods [of knitting]. I’ve been in factories, for instance in New Jersey, where all they had ever done was cut-and-sew. There, we were trying to introduce to looping machines so they could make technically ‘hybrid’ sweaters—we would cut-and-sew (overlock the edges of the knitted pieces) the neck shaping, and then loop over that so it’s perfectly secure, and perfectly good-looking. I think it’s really important to take the machine capabilities that you’re faced with–and think of ways to enhance them.
But the big difference [between cut-and-sew sweaters & fully-fashioned ones] is that you pay someone more to work on a hand-frame machine. There’s a lot of skill involved in hand-framed full-fashioning, manipulating the stitches with the little tools to make component parts with the correct outlines. You also have to do a lot of work up front—the math and tension swatches–you know, there has to be a lot of technical prep. It’s a lot more expensive to make a fully-fashioned garment.
Crochet versus fully-fashioned knit–what’s a quick definition of the difference between the two?
Crochet is a completely different skill [than knitting]; it’s a different technique entirely. It’s much slower, on the whole. You’ve got one hook and one yarn source and you’re basically making a continuous chain and manipulating that chain into various patterns. So it’s very laborious. I saw a full-length crocheted skirt the other day for $70. I don’t know how that can be ethically made. If it was knitted, it could be made very quickly on a machine but with crochet, there’s no machine to exactly duplicate that technique.
Are there designers / small labels that you think are priced appropriately for the labor and quality they’re offering?
Everyone loves a bargain, but consumers are also concerned about fair wages and ethical practices in the clothing industry. If you’re privy to everything that goes into designing, technicalizing, manufacturing, packing, shipping and selling a sweater, you know how difficult it is to control the pricing - especially recently! Sometimes you just can’t make the pricing work. When I opened my workshop in Oak Hill, complete with retail space if I wanted it in the store below, all I could think about was using yarn from Greene County sheep (who were as close as 3 miles away!) and operating the perfect, sustainable local manufacturing set up. But the costs were very high. I produced some gorgeous accessories, but sweaters have to be specially ordered for it to make sense in my situation.
Small batch production is never going to be inexpensive and knitting is so labor-intensive, you have to somehow be covered for all the time you put in. I love that I have access occasionally to people who want to spend money on my skills, so I can make a special piece for them - so we’re both profiting from it. That’s often when you can put into practice an original technique or stitch or application you’ve come up with that just can’t be used efficiently in a manufacturing context - it just looks great. As for the designers question - I like Bode’s knitwear a lot.
Are there design details or yarn contents that you feel cut corners on quality or ethics? The “coffin sweater” term you told me about years ago, for example, always made me laugh…
A coffin sweater is when a sweater has a plain back to save on construction cost, i.e. it may have a cable-knit stitch on the front and plain jersey stitch on the back. If you’re laying in your coffin, no one sees it, so who cares if it’s under-designed compared to the front lol…
I don’t blame people for cutting corners, in order to try and manage the pricing - you know, I mean…there’s a place for everything. During my 7th Avenue years I got very good at reducing sweater costs using my technical skills – I think that’s why I got hired a lot of times back in the day. Without taking away any of the perceived quality I was able to make something more affordable and that always felt great. Of course nowadays we think much more about sustainability and then it was all about volume. It’s great that we’re all still buying a lot of vintage. There’s still so much stuff out there to be made use of!
Right. That’s where the “patch & mend”, not throwaway mentality comes into play, [part of our Villeine mission statement]. Because there is so much life left for a lot of these sweaters, even with holes or whatnot.
Absolutely! The whole idea of renovating things…I got totally lost in that for about six months a couple of years ago. Just finding vintage, or not even vintage sweaters, and just picking them apart and re-inventing. It was yet another set of endless possibilities, which is something so relevant to knitting because you know, knitting structure–there’s only knit, tuck and transfer–that’s all you can do, three things….and out of those three principle actions, everything you’ve ever seen that’s knitted came to be.
Follow Sue on Instagram for more knitwear tokens, @makersofmanners & the Oak Hill, NY boutique where her studio is located above @mattice.boutique

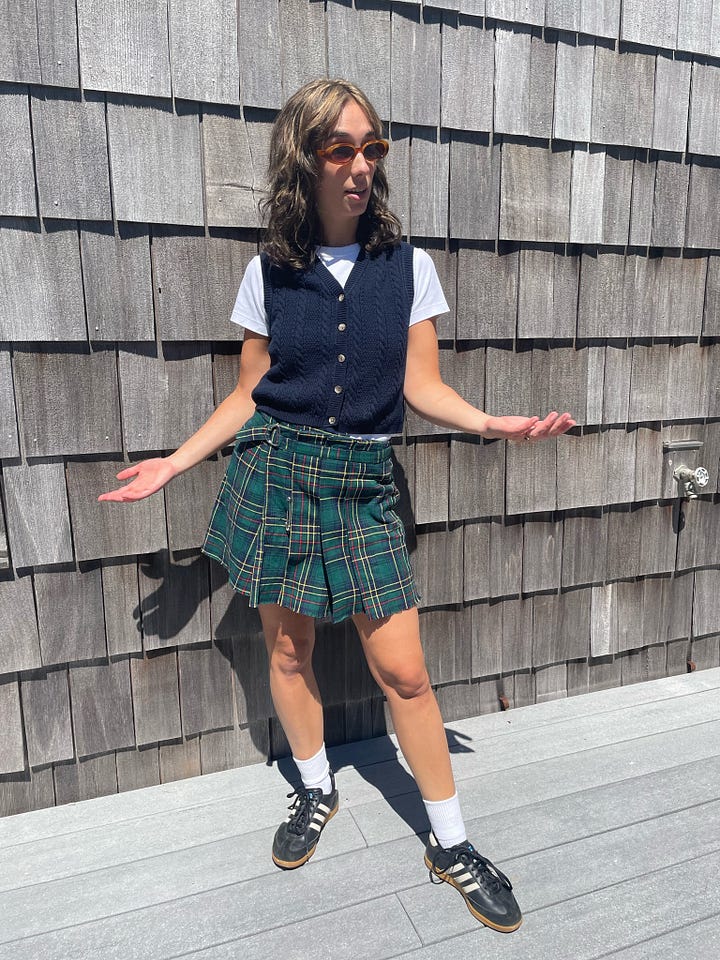
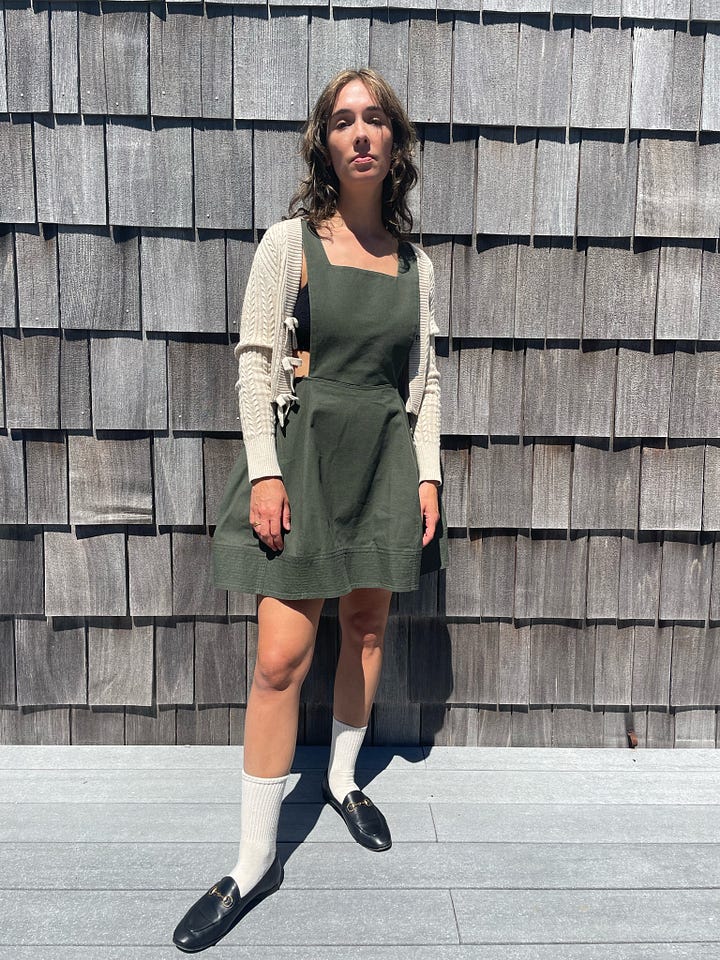
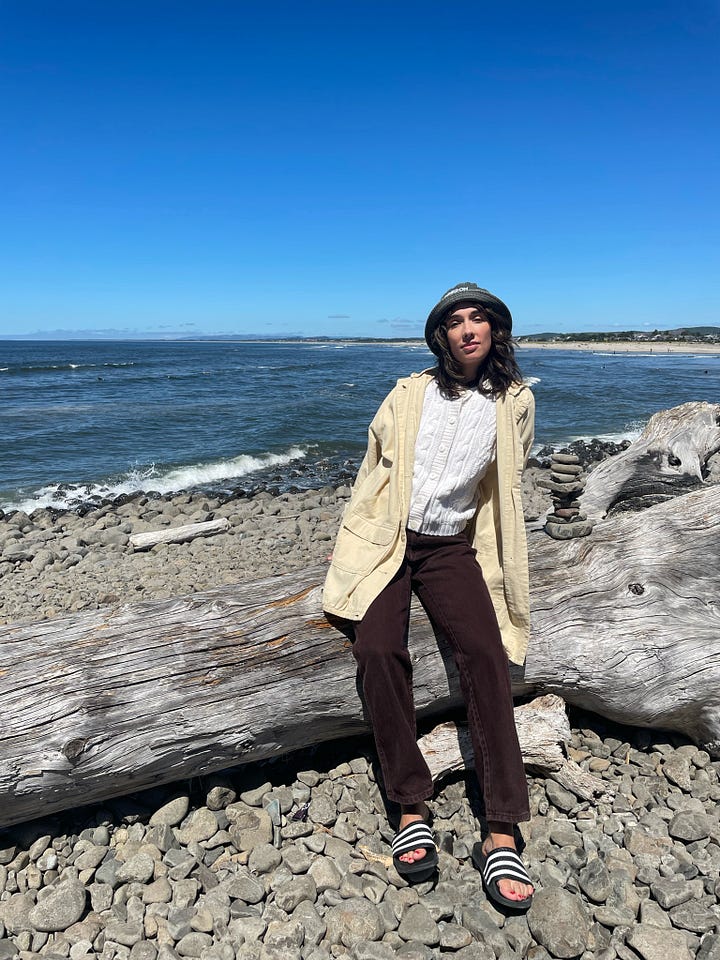
I’m wearing: 1) vintage crochet shawl made in Nepal with my Villeine LeRoy Overall in Oatmeal; 2) vintage Liz Sport cable knit (coffin sweater) vest w/ thrifted kilt; 3) Rachel Antonoff Sosia bow-detail cable knit (all around :) cardigan Sue & I developed together (made in Peru) w/ Villeine Orthena Pinafore Dress; 4) vintage Eddie Bauer cable knit (coffin sweater) cardigan that has cut-and-sew 1980s’ construction w/ vintage Dickies & Woolrich painter’s smock jacket.
Missing from my suitcase are crochet and/or knitted polos—an essential summer knit.
Jude Law in “The Talented Mr. Ripley” (1999)
Sarah Jessica Parker as Carrie Bradshaw in “Sex & the City” season 3, (2000)
Agnes B. cut-and-sew knitted snap-front cardigan made in France $225
Baserange linen blend rib fully fashioned cardigan made in Portugal $206.50
Maiden Name made in USA space dyed cut-and-sew rib knit cardigan $177
A big thanks to Sue for the interview and her unfathomable amount of knowledge on knitwear…after this, I’m considering an “ask Sue about knits” recurring section for CRACD. Wishing you well from my family reunion in beautiful Seaside, OR this week. xHannah
I learned so much about knits. Thank you Sue and Hannah—I realize now that I have several “coffin sweaters”!